تعتبر تقنية تقطيع الرقاقة، كخطوة أساسية في عملية تصنيع أشباه الموصلات، مرتبطة بشكل مباشر بأداء الرقاقة، والعائد، وتكاليف الإنتاج.
#01 خلفية وأهمية تقطيع الرقاقات
1.1 تعريف تقطيع الرقاقات
يُعدّ تقطيع الرقاقات (المعروف أيضًا بالنقش) خطوةً أساسيةً في تصنيع أشباه الموصلات، ويهدف إلى تقسيم الرقاقات المُعالجة إلى عدة قوالب فردية. عادةً ما تحتوي هذه القوالب على وظائف الدوائر المتكاملة، وهي المكونات الأساسية المستخدمة في إنتاج الأجهزة الإلكترونية. مع ازدياد تعقيد تصميمات الرقاقات وتقلص أبعادها باستمرار، تزداد متطلبات الدقة والكفاءة لتقنية تقطيع الرقاقات صرامةً.
في العمليات العملية، عادةً ما تستخدم عملية تقطيع الرقاقات أدوات عالية الدقة، مثل شفرات الماس، لضمان سلامة كل قالب وكفاءته. تشمل الخطوات الرئيسية التحضير قبل القطع، والمراقبة الدقيقة أثناء عملية القطع، وفحص الجودة بعد القطع.
قبل القطع، يجب وضع علامات على الرقاقة وتحديد موضعها لضمان دقة مسارات القطع. أثناء القطع، يجب مراقبة معايير مثل ضغط الأداة وسرعتها بدقة لمنع تلف الرقاقة. بعد القطع، تُجرى فحوصات جودة شاملة لضمان استيفاء كل رقاقة لمعايير الأداء.
لا تقتصر المبادئ الأساسية لتقنية تقطيع الرقاقات على اختيار معدات القطع وضبط معايير العملية فحسب، بل تشمل أيضًا تأثير الخصائص الميكانيكية وخصائص المواد على جودة القطع. على سبيل المثال، تُعدّ رقاقات السيليكون العازلة منخفضة معامل الكفاءة (K)، نظرًا لخصائصها الميكانيكية المتدنية، شديدة التأثر بتركيز الإجهاد أثناء القطع، مما يؤدي إلى أعطال مثل التقطيع والتشقق. كما أن انخفاض صلابة وهشاشة المواد منخفضة معامل الكفاءة (K) يجعلها أكثر عرضة للتلف الهيكلي تحت تأثير القوة الميكانيكية أو الإجهاد الحراري، وخاصةً أثناء القطع. ويمكن أن يؤدي تلامس الأداة مع سطح الرقاقة، بالإضافة إلى درجات الحرارة المرتفعة، إلى تفاقم تركيز الإجهاد.
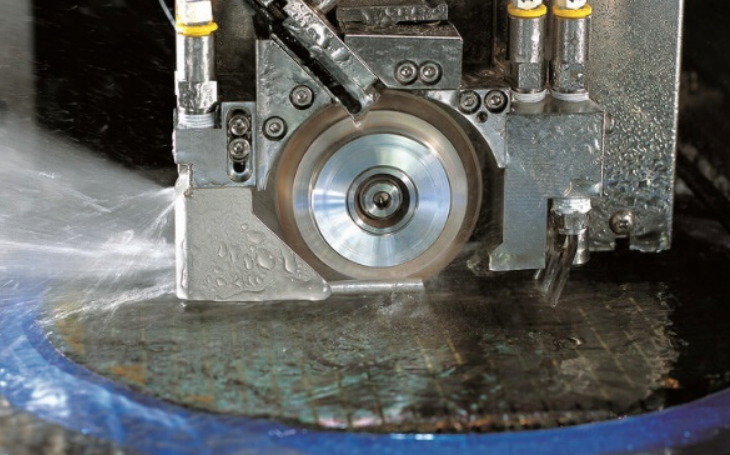
مع التقدم في علوم المواد، توسعت تقنية تقطيع الرقاقات لتتجاوز أشباه الموصلات التقليدية القائمة على السيليكون لتشمل مواد جديدة مثل نتريد الغاليوم (GaN). تُشكل هذه المواد الجديدة، نظرًا لصلابتها وخصائصها البنيوية، تحديات جديدة لعمليات التقطيع، مما يتطلب تحسينات إضافية في أدوات وتقنيات القطع.
باعتبارها عملية بالغة الأهمية في صناعة أشباه الموصلات، تستمر عملية تقطيع الرقائق في التحسن استجابةً للطلبات المتطورة والتقدم التكنولوجي، مما يضع الأساس لتقنيات الإلكترونيات الدقيقة والدوائر المتكاملة في المستقبل.
تتجاوز التحسينات في تقنية تقطيع الرقاقات تطوير المواد والأدوات المساعدة، بل تشمل أيضًا تحسين العمليات، وتحسين أداء المعدات، والتحكم الدقيق في معاملات التقطيع. تهدف هذه التطورات إلى ضمان دقة وكفاءة واستقرار عاليين في عملية تقطيع الرقاقات، مما يلبي حاجة صناعة أشباه الموصلات إلى أبعاد أصغر، وتكامل أعلى، وهياكل رقائق أكثر تعقيدًا.
منطقة التحسين | تدابير محددة | التأثيرات |
تحسين العمليات | - تحسين الاستعدادات الأولية، مثل تحديد موضع الرقاقة بشكل أكثر دقة وتخطيط المسار. | - تقليل أخطاء القطع وتحسين الاستقرار. |
- تقليل أخطاء القطع وتعزيز الاستقرار. | - اعتماد آليات المراقبة والتغذية الراجعة في الوقت الفعلي لضبط ضغط الأداة وسرعتها ودرجة حرارتها. | |
- انخفاض معدلات كسر الرقاقة وتحسين جودة الرقاقة. | ||
تحسين أداء المعدات | - استخدام أنظمة ميكانيكية عالية الدقة وتكنولوجيا التحكم الآلي المتقدمة. | - تعزيز دقة القطع وتقليل هدر المواد. |
- إدخال تقنية القطع بالليزر المناسبة لرقائق المواد ذات الصلابة العالية. | - تحسين كفاءة الإنتاج وتقليل الأخطاء اليدوية. | |
- زيادة أتمتة المعدات للمراقبة والتعديلات التلقائية. | ||
التحكم الدقيق في المعلمات | - ضبط المعلمات بدقة مثل عمق القطع والسرعة ونوع الأداة وطرق التبريد. | - التأكد من سلامة القالب والأداء الكهربائي. |
- تخصيص المعلمات بناءً على مادة الرقاقة وسمكها وبنيتها. | - تعزيز معدلات العائد، وتقليل هدر المواد، وخفض تكاليف الإنتاج. | |
الأهمية الاستراتيجية | - استكشاف المسارات التكنولوجية الجديدة بشكل مستمر، وتحسين العمليات، وتعزيز قدرات المعدات لتلبية متطلبات السوق. | - تحسين إنتاجية وأداء تصنيع الرقائق، ودعم تطوير مواد جديدة وتصاميم رقائق متقدمة. |
1.2 أهمية تقطيع الرقاقات
يلعب تقطيع الرقاقات دورًا حاسمًا في عملية تصنيع أشباه الموصلات، إذ يؤثر بشكل مباشر على الخطوات اللاحقة، بالإضافة إلى جودة وأداء المنتج النهائي. ويمكن تفصيل أهميته على النحو التالي:
أولاً، تُعدّ دقة وتناسق عملية التقطيع أمرًا أساسيًا لضمان إنتاجية الشريحة وموثوقيتها. أثناء التصنيع، تخضع الرقائق لخطوات معالجة متعددة لتشكيل هياكل دوائر متعددة ومعقدة، والتي يجب تقسيمها بدقة إلى شرائح (قوالب) فردية. في حال وجود أخطاء كبيرة في المحاذاة أو القطع أثناء عملية التقطيع، فقد تتلف الدوائر، مما يؤثر على وظائف الشريحة وموثوقيتها. لذلك، لا تضمن تقنية التقطيع عالية الدقة سلامة كل شريحة فحسب، بل تمنع أيضًا تلف الدوائر الداخلية، مما يُحسّن معدل الإنتاج الإجمالي.
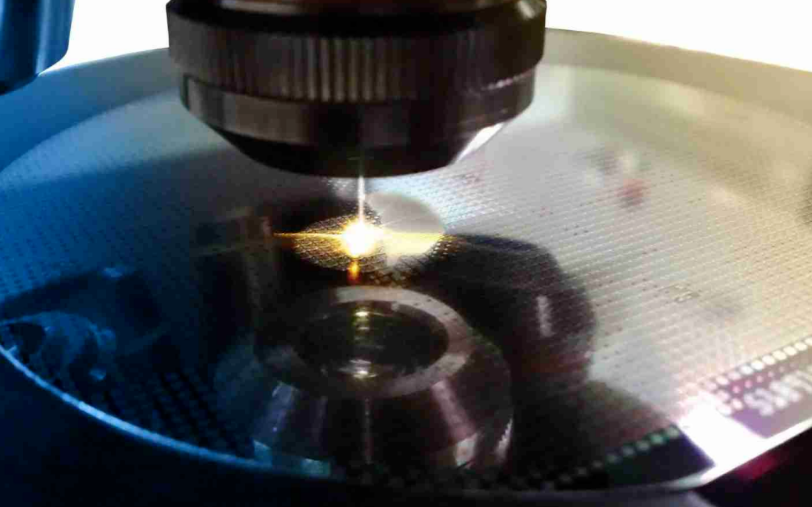
ثانيًا، لتقطيع الرقاقات تأثير كبير على كفاءة الإنتاج وضبط التكاليف. وباعتبارها خطوةً حاسمةً في عملية التصنيع، تؤثر كفاءتها بشكل مباشر على تقدم الخطوات اللاحقة. ومن خلال تحسين عملية التقطيع، وزيادة مستويات الأتمتة، وتحسين سرعات القطع، يمكن تعزيز كفاءة الإنتاج الإجمالية بشكل كبير.
من ناحية أخرى، يُعدّ هدر المواد أثناء التقطيع عاملاً حاسماً في إدارة التكاليف. ولا يقتصر استخدام تقنيات التقطيع المتقدمة على تقليل خسائر المواد غير الضرورية أثناء عملية التقطيع، بل يزيد أيضاً من كفاءة استخدام الرقاقة، مما يُخفّض تكاليف الإنتاج.
مع التقدم في تكنولوجيا أشباه الموصلات، تستمر أقطار الرقاقات في التزايد، وترتفع بالتالي كثافة الدوائر، مما يزيد من متطلبات تقنية التقطيع. تتطلب الرقاقات الأكبر حجمًا تحكمًا أكثر دقة في مسارات القطع، خاصةً في مناطق الدوائر عالية الكثافة، حيث قد تؤدي حتى الانحرافات الطفيفة إلى تعطل العديد من الرقاقات. بالإضافة إلى ذلك، تتطلب الرقاقات الأكبر حجمًا خطوط قطع أكثر وخطوات عملية أكثر تعقيدًا، مما يستلزم تحسينات إضافية في دقة واتساق وكفاءة تقنيات التقطيع لمواجهة هذه التحديات.
1.3 عملية تقطيع الرقاقة
تشمل عملية تقطيع رقائق الويفر جميع الخطوات، من مرحلة التحضير إلى فحص الجودة النهائي، حيث تُعدّ كل مرحلة حاسمة لضمان جودة وأداء رقائق الويفر المُقطّعة. فيما يلي شرح مُفصّل لكل مرحلة.
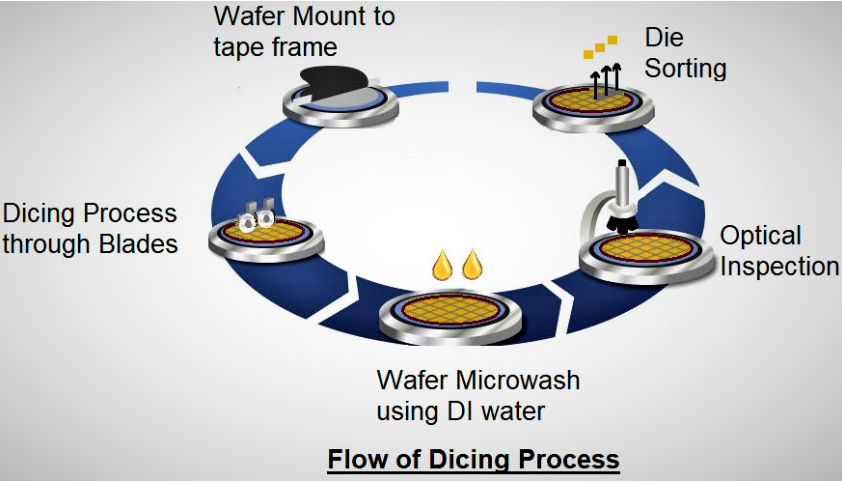
مرحلة | الوصف التفصيلي |
مرحلة التحضير | -تنظيف الرقاقة:استخدم الماء عالي النقاء ومواد التنظيف المتخصصة، جنبًا إلى جنب مع التنظيف بالموجات فوق الصوتية أو الميكانيكية، لإزالة الشوائب والجزيئات والمواد الملوثة، مما يضمن سطحًا نظيفًا. -تحديد المواقع بدقة:استخدم معدات عالية الدقة لضمان تقسيم الرقاقة بدقة على طول مسارات القطع المصممة. -تثبيت الرقاقة:قم بتأمين الرقاقة على إطار الشريط للحفاظ على الاستقرار أثناء القطع، ومنع التلف الناتج عن الاهتزاز أو الحركة. |
مرحلة القطع | -تقطيع النصل:استخدم شفرات دوارة عالية السرعة مغطاة بالماس للقطع المادي، وهي مناسبة للمواد القائمة على السيليكون وفعالة من حيث التكلفة. -تقطيع بالليزر:استخدم أشعة الليزر عالية الطاقة للقطع بدون تلامس، وهي مثالية للمواد الهشة أو ذات الصلابة العالية مثل نتريد الجاليوم، مما يوفر دقة أعلى وخسارة أقل للمواد. -التقنيات الجديدة:إدخال تقنيات القطع بالليزر والبلازما لتحسين الكفاءة والدقة بشكل أكبر مع تقليل المناطق المتأثرة بالحرارة. |
مرحلة التنظيف | - استخدام الماء منزوع الأيونات (ماء DI) وعوامل التنظيف المتخصصة، جنبًا إلى جنب مع التنظيف بالموجات فوق الصوتية أو الرش، لإزالة الحطام والغبار الناتج أثناء القطع، ومنع البقايا من التأثير على العمليات اللاحقة أو الأداء الكهربائي للشريحة. - تتجنب مياه DI عالية النقاء إدخال ملوثات جديدة، مما يضمن بيئة رقاقة نظيفة. |
مرحلة التفتيش | -التفتيش البصري:استخدام أنظمة الكشف البصري جنبًا إلى جنب مع خوارزميات الذكاء الاصطناعي لتحديد العيوب بسرعة، مما يضمن عدم وجود شقوق أو تشققات في الرقائق المقطعة، وتحسين كفاءة التفتيش، والحد من الخطأ البشري. -قياس الأبعاد:تأكد من أن أبعاد الشريحة تتوافق مع مواصفات التصميم. -اختبار الأداء الكهربائي:تأكد من أن الأداء الكهربائي للشرائح المهمة يفي بالمعايير، مما يضمن الموثوقية في التطبيقات اللاحقة. |
مرحلة الفرز | - استخدام الأذرع الروبوتية أو أكواب الشفط الفراغية لفصل الرقائق المؤهلة عن إطار الشريط وفرزها تلقائيًا بناءً على الأداء، مما يضمن كفاءة الإنتاج والمرونة مع تحسين الدقة. |
تتضمن عملية قطع الرقاقة تنظيفها، وتحديد موضعها، وقطعها، وتنظيفها، وفحصها، وفرزها، وكل خطوة بالغة الأهمية. مع التطورات في الأتمتة، والقطع بالليزر، وتقنيات فحص الذكاء الاصطناعي، يمكن لأنظمة قطع الرقاقة الحديثة تحقيق دقة وسرعة أعلى، وتقليل فقد المواد. في المستقبل، ستحل تقنيات القطع الجديدة، مثل الليزر والبلازما، تدريجيًا محل القطع التقليدي بالشفرة لتلبية احتياجات تصميمات الرقاقات المتزايدة التعقيد، مما يدفع عجلة تطوير عمليات تصنيع أشباه الموصلات.
تقنية قطع الرقاقة ومبادئها
توضح الصورة ثلاث تقنيات شائعة لقطع الرقاقة:تقطيع النصل،تقطيع بالليزر، وتقطيع البلازمافيما يلي تحليل مفصل وشرح إضافي لهذه التقنيات الثلاث:
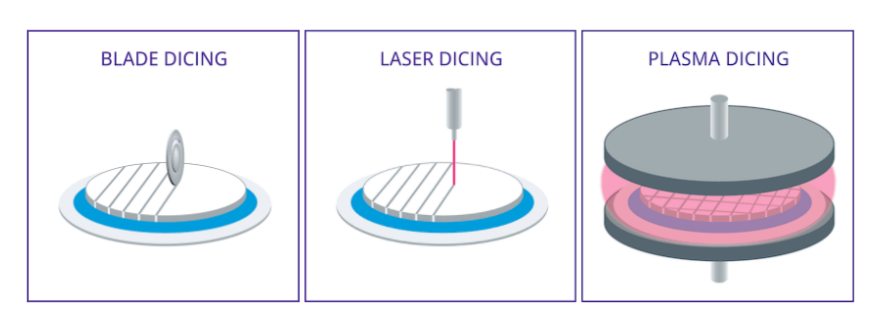
في تصنيع أشباه الموصلات، يُعدّ قطع الرقاقة خطوةً حاسمةً تتطلب اختيار طريقة القطع المناسبة بناءً على سُمكها. الخطوة الأولى هي تحديد سُمك الرقاقة. إذا تجاوز سُمك الرقاقة 100 ميكرون، يُمكن اختيار تقطيع الشفرات كطريقة للقطع. إذا لم يكن تقطيع الشفرات مناسبًا، يُمكن استخدام طريقة تقطيع الكسر، والتي تشمل تقنيتي تقطيع الشفرات والقطع بالخطاطيف.
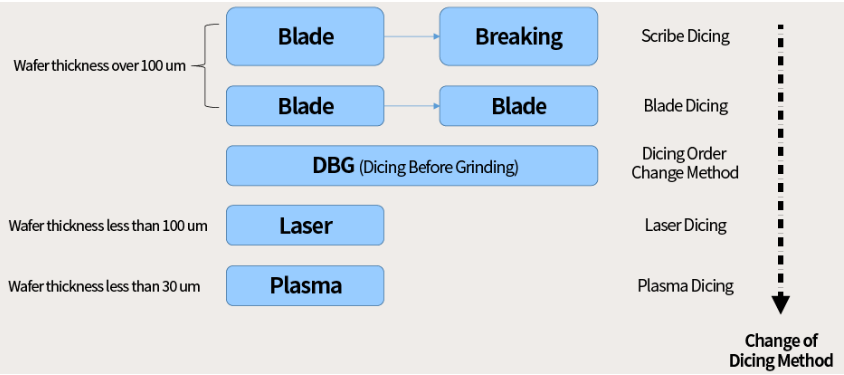
عندما يتراوح سُمك الرقاقة بين 30 و100 ميكرون، يُنصح باستخدام طريقة DBG (التقطيع قبل الطحن). في هذه الحالة، يُمكن اختيار القطع بالنقش، أو التقطيع بالشفرة، أو تعديل تسلسل القطع حسب الحاجة لتحقيق أفضل النتائج.
بالنسبة للرقائق فائقة الرقة التي يقل سمكها عن 30 ميكرون، يُعدّ القطع بالليزر الطريقة المُفضّلة نظرًا لقدرته على قطع الرقائق الرقيقة بدقة دون التسبب في أضرار جسيمة. إذا لم يُلبِّ القطع بالليزر متطلبات مُحدّدة، يُمكن استخدام القطع بالبلازما كبديل. يُقدّم هذا المخطط الانسيابي مسارًا واضحًا لاتخاذ القرارات لضمان اختيار تقنية قطع الرقائق الأنسب في ظلّ ظروف سُمك مُختلفة.
2.1 تكنولوجيا القطع الميكانيكية
تقنية القطع الميكانيكية هي الطريقة التقليدية لتقطيع الرقاقات. وتقوم على استخدام عجلة طحن ماسية دوارة عالية السرعة كأداة قطع لتقطيع الرقاقة. وتتضمن المعدات الرئيسية مغزلًا هوائيًا، يُحرك عجلة طحن الماس بسرعات عالية لإجراء قطع أو حفر دقيق على مسار قطع محدد مسبقًا. وتُستخدم هذه التقنية على نطاق واسع في الصناعة نظرًا لتكلفتها المنخفضة وكفاءتها العالية وإمكانية تطبيقها على نطاق واسع.
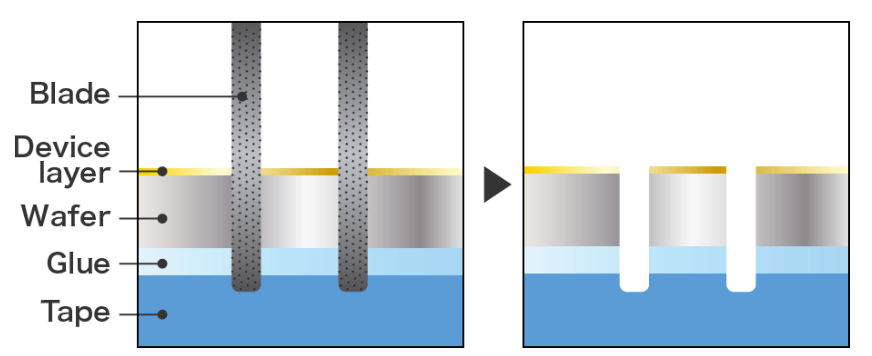
المزايا
بفضل صلابة أدوات طحن الماس العالية ومقاومتها العالية للتآكل، تُمكّن تقنية القطع الميكانيكي من تلبية احتياجات قطع مختلف مواد الرقاقات، سواءً كانت مواد تقليدية قائمة على السيليكون أو أشباه موصلات مركبة حديثة. وتتميز هذه التقنية بسهولة تشغيلها ومتطلباتها التقنية المنخفضة نسبيًا، مما يعزز شعبيتها في الإنتاج الضخم. بالإضافة إلى ذلك، بالمقارنة مع طرق القطع الأخرى، مثل القطع بالليزر، يتميز القطع الميكانيكي بتكاليف أقل، مما يجعله مناسبًا لاحتياجات الإنتاج بكميات كبيرة.
القيود
على الرغم من مزاياها العديدة، إلا أن لتقنية القطع الميكانيكي بعض القيود. أولًا، نظرًا للتلامس المادي بين الأداة والرقاقة، تكون دقة القطع محدودة نسبيًا، مما يؤدي غالبًا إلى انحرافات في الأبعاد قد تؤثر على دقة تغليف الرقاقة واختبارها لاحقًا. ثانيًا، قد تظهر عيوب مثل التشقق والتشققات بسهولة أثناء عملية القطع الميكانيكي، مما لا يؤثر فقط على معدل العائد، بل قد يؤثر سلبًا أيضًا على موثوقية الرقاقات وعمرها الافتراضي. يُعد الضرر الناتج عن الإجهاد الميكانيكي ضارًا بشكل خاص بتصنيع الرقاقات عالية الكثافة، وخاصةً عند قطع المواد الهشة، حيث تكون هذه المشاكل أكثر وضوحًا.
التحسينات التكنولوجية
للتغلب على هذه القيود، يعمل الباحثون باستمرار على تحسين عملية القطع الميكانيكية. تشمل التحسينات الرئيسية تحسين تصميم واختيار مواد عجلات الطحن لتحسين دقة القطع ومتانته. بالإضافة إلى ذلك، أدى تحسين التصميم الهيكلي وأنظمة التحكم في معدات القطع إلى تحسين استقرار عملية القطع وأتمتتها. تقلل هذه التطورات من الأخطاء الناتجة عن العمليات البشرية، وتُحسّن اتساق القطع. كما أدى إدخال تقنيات متقدمة للفحص ومراقبة الجودة للرصد الفوري لأي تشوهات أثناء عملية القطع إلى تحسين موثوقية القطع وإنتاجيته بشكل ملحوظ.
التطوير المستقبلي والتقنيات الجديدة
على الرغم من أن تقنية القطع الميكانيكي لا تزال تحتل مكانة بارزة في قطع الرقاقات، إلا أن تقنيات القطع الجديدة تتطور بسرعة مع تطور عمليات أشباه الموصلات. على سبيل المثال، يوفر تطبيق تقنية القطع بالليزر الحراري حلولاً جديدة لمشاكل الدقة والعيوب في القطع الميكانيكي. تُقلل طريقة القطع غير التلامسية هذه من الضغط المادي على الرقاقة، مما يُقلل بشكل كبير من احتمالية التشقق والتشقق، خاصةً عند قطع المواد الأكثر هشاشة. في المستقبل، سيوفر دمج تقنية القطع الميكانيكي مع تقنيات القطع الناشئة خيارات ومرونة أكبر لتصنيع أشباه الموصلات، مما يُعزز كفاءة التصنيع وجودة الرقاقة.
وفي الختام، وعلى الرغم من أن تكنولوجيا القطع الميكانيكية لها بعض العيوب، فإن التحسينات التكنولوجية المستمرة وتكاملها مع تقنيات القطع الجديدة تسمح لها بلعب دور مهم في تصنيع أشباه الموصلات والحفاظ على قدرتها التنافسية في العمليات المستقبلية.
2.2 تقنية القطع بالليزر
اكتسبت تقنية القطع بالليزر، كطريقة جديدة لقطع الرقاقات، اهتمامًا متزايدًا في صناعة أشباه الموصلات بفضل دقتها العالية، وقلة أضرار التلامس الميكانيكي، وسرعة قطعها. تستخدم هذه التقنية كثافة الطاقة العالية وقدرة تركيز شعاع الليزر لإنشاء منطقة صغيرة متأثرة بالحرارة على سطح مادة الرقاقة. عند تسليط شعاع الليزر على الرقاقة، يتسبب الإجهاد الحراري الناتج في كسر المادة في الموقع المحدد، مما يحقق قطعًا دقيقًا.
مزايا تقنية القطع بالليزر
• دقة عالية:تتيح قدرة تحديد المواقع الدقيقة لشعاع الليزر دقة القطع على مستوى الميكرون أو حتى النانومتر، مما يلبي متطلبات تصنيع الدوائر المتكاملة الحديثة عالية الدقة وعالية الكثافة.
• لا يوجد اتصال ميكانيكي:تتجنب عملية القطع بالليزر الاتصال المادي بالرقاقة، مما يمنع المشكلات الشائعة في القطع الميكانيكي، مثل التقطيع والتشقق، مما يحسن بشكل كبير معدل العائد وموثوقية الرقائق.
• سرعة القطع السريعة:تساهم السرعة العالية للقطع بالليزر في زيادة كفاءة الإنتاج، مما يجعلها مناسبة بشكل خاص لسيناريوهات الإنتاج عالية السرعة وعلى نطاق واسع.
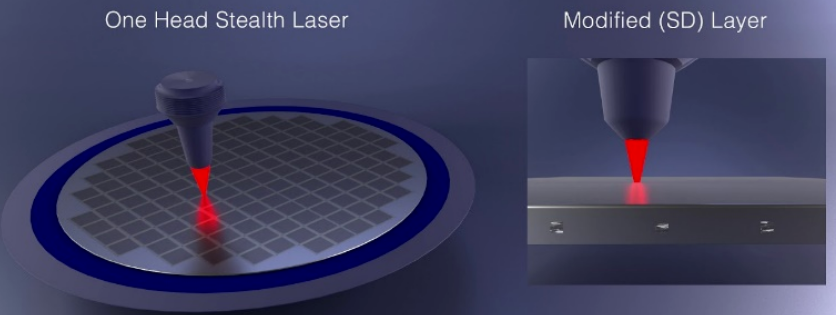
التحديات التي واجهتها
• تكلفة المعدات العالية:إن الاستثمار الأولي لمعدات القطع بالليزر مرتفع، مما يشكل ضغطًا اقتصاديًا، خاصة بالنسبة لمؤسسات الإنتاج الصغيرة والمتوسطة الحجم.
• التحكم في العمليات المعقدة:يتطلب القطع بالليزر التحكم الدقيق في العديد من المعلمات، بما في ذلك كثافة الطاقة، وموضع التركيز، وسرعة القطع، مما يجعل العملية معقدة.
• مشاكل المناطق المتأثرة بالحرارةعلى الرغم من أن طبيعة القطع بالليزر غير التلامسية تُقلل من الضرر الميكانيكي، إلا أن الإجهاد الحراري الناتج عن المنطقة المتأثرة بالحرارة (HAZ) قد يؤثر سلبًا على خصائص مادة الرقاقة. ويلزم تحسين العملية بشكل أكبر لتقليل هذا التأثير.
اتجاهات التحسين التكنولوجي
ولمعالجة هذه التحديات، يركز الباحثون على خفض تكاليف المعدات، وتحسين كفاءة القطع، وتحسين سير العملية.
• أنظمة الليزر والبصريات الفعالة:من خلال تطوير أجهزة الليزر الأكثر كفاءة والأنظمة البصرية المتقدمة، من الممكن خفض تكاليف المعدات مع تعزيز دقة القطع وسرعته.
• تحسين معلمات العملية:يتم إجراء أبحاث معمقة حول التفاعل بين الليزر ومواد الرقاقة لتحسين العمليات التي تقلل من المنطقة المتأثرة بالحرارة، وبالتالي تحسين جودة القطع.
• أنظمة التحكم الذكية:يهدف تطوير تقنيات التحكم الذكية إلى أتمتة وتحسين عملية القطع بالليزر، وتحسين استقرارها وتناسقها.
تتميز تقنية القطع بالليزر بفعالية خاصة في الرقاقات فائقة الرقة وفي سيناريوهات القطع عالية الدقة. ومع ازدياد أحجام الرقاقات وارتفاع كثافة الدوائر، تواجه طرق القطع الميكانيكية التقليدية صعوبة في تلبية متطلبات الدقة والكفاءة العالية في تصنيع أشباه الموصلات الحديثة. وبفضل مزاياها الفريدة، أصبح القطع بالليزر الحل الأمثل في هذه المجالات.
على الرغم من أن تقنية القطع بالليزر لا تزال تواجه تحدياتٍ مثل ارتفاع تكاليف المعدات وتعقيد العمليات، إلا أن مزاياها الفريدة في الدقة العالية وعدم التلامس تجعلها توجهًا مهمًا لتطوير صناعة أشباه الموصلات. ومع استمرار تطور تكنولوجيا الليزر وأنظمة التحكم الذكية، من المتوقع أن يُحسّن القطع بالليزر كفاءة وجودة قطع الرقاقات، مما يُعزز التطور المستمر لصناعة أشباه الموصلات.
2.3 تقنية القطع بالبلازما
اكتسبت تقنية قطع البلازما، كطريقة ناشئة لتقطيع الرقاقات، اهتمامًا كبيرًا في السنوات الأخيرة. تستخدم هذه التقنية أشعة بلازما عالية الطاقة لقطع الرقاقات بدقة من خلال التحكم في طاقة شعاع البلازما وسرعته ومسار قطعه، مما يحقق نتائج قطع مثالية.
مبدأ العمل والمزايا
تعتمد عملية القطع بالبلازما على شعاع بلازما عالي الحرارة والطاقة يُولّده الجهاز. يُسخّن هذا الشعاع مادة الرقاقة إلى درجة الانصهار أو التبخر في وقت قصير جدًا، مما يُتيح قطعًا سريعًا. مقارنةً بالقطع الميكانيكي أو الليزري التقليدي، يتميز القطع بالبلازما بسرعة أكبر ويُنتج منطقة أصغر متأثرة بالحرارة، مما يُقلل بشكل فعال من حدوث التشققات والتلف أثناء القطع.
في التطبيقات العملية، تتميز تقنية القطع بالبلازما بكفاءتها العالية في التعامل مع الرقائق ذات الأشكال المعقدة. شعاع البلازما عالي الطاقة والقابل للتعديل قادر على قطع الرقائق غير المنتظمة بسهولة ودقة عالية. لذلك، في تصنيع الإلكترونيات الدقيقة، وخاصةً في إنتاج الرقائق عالية الجودة حسب الطلب وعلى دفعات صغيرة، تُبشّر هذه التقنية بإمكانية استخدامها على نطاق واسع.
التحديات والقيود
على الرغم من المزايا العديدة لتكنولوجيا القطع بالبلازما، إلا أنها تواجه أيضًا بعض التحديات.
• عملية معقدة:إن عملية قطع البلازما معقدة وتتطلب معدات عالية الدقة ومشغلين ذوي خبرة لضمانالدقة والاستقرار في القطع.
• الرقابة البيئية والسلامة:تتطلب طبيعة شعاع البلازما عالية الحرارة وعالية الطاقة إجراءات صارمة للتحكم البيئي وتدابير السلامة، مما يزيد من تعقيد وتكلفة التنفيذ.
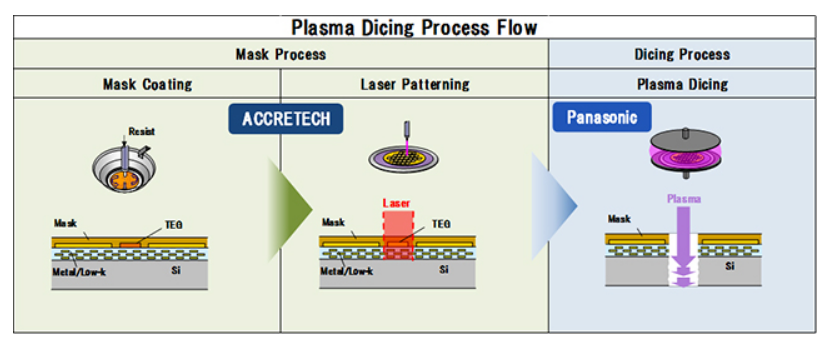
اتجاهات التطوير المستقبلية
مع التقدم التكنولوجي، من المتوقع التغلب تدريجيًا على تحديات القطع بالبلازما. ومن خلال تطوير معدات قطع أكثر ذكاءً واستقرارًا، يمكن تقليل الاعتماد على العمليات اليدوية، مما يُحسّن كفاءة الإنتاج. وفي الوقت نفسه، يُسهم تحسين معايير العملية وبيئة القطع في خفض مخاطر السلامة وتكاليف التشغيل.
في صناعة أشباه الموصلات، تُعدّ الابتكارات في تقنيات تقطيع وتقطيع الرقاقات أمرًا بالغ الأهمية لدفع عجلة تطوير هذه الصناعة. وقد برزت تقنية تقطيع البلازما، بدقتها العالية وكفاءتها العالية وقدرتها على التعامل مع أشكال الرقاقات المعقدة، كلاعب جديد ومهم في هذا المجال. ورغم استمرار بعض التحديات، إلا أنه سيتم معالجتها تدريجيًا مع استمرار الابتكار التكنولوجي، مما يوفر إمكانيات وفرصًا أكبر لتصنيع أشباه الموصلات.
آفاق تطبيق تقنية القطع بالبلازما واسعة، ومن المتوقع أن تلعب دورًا أكثر أهمية في تصنيع أشباه الموصلات مستقبلًا. ومن خلال الابتكار التكنولوجي المستمر والتحسين، لن يقتصر دور القطع بالبلازما على معالجة التحديات القائمة فحسب، بل سيصبح أيضًا محركًا قويًا لنمو صناعة أشباه الموصلات.
2.4 جودة القطع والعوامل المؤثرة
جودة قطع الرقاقة أساسية لتغليف الرقاقة لاحقًا، واختبارها، والأداء العام وموثوقية المنتج النهائي. من المشاكل الشائعة التي تُواجه أثناء القطع التشققات والتقطيع وانحرافات القطع. تتأثر هذه المشاكل بعدة عوامل تتداخل معًا.
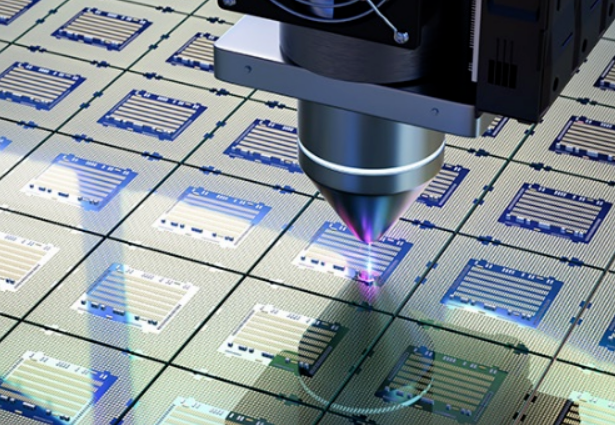
فئة | محتوى | تأثير |
معلمات العملية | تؤثر سرعة القطع ومعدل التغذية وعمق القطع بشكل مباشر على استقرار ودقة عملية القطع. قد تؤدي الإعدادات غير الصحيحة إلى تركيز الإجهاد وزيادة منطقة التأثر بالحرارة، مما يؤدي إلى تشققات وتقطيع. يُعد ضبط المعلمات بشكل مناسب بناءً على مادة الرقاقة وسمكها ومتطلبات القطع أمرًا أساسيًا لتحقيق نتائج القطع المرجوة. | تضمن معلمات العملية الصحيحة القطع الدقيق وتقليل خطر العيوب مثل الشقوق والتقطيع. |
عوامل المعدات والمواد | -جودة الشفرةتؤثر مادة الشفرة وصلابتها ومقاومتها للتآكل على سلاسة عملية القطع واستواء سطح القطع. تؤدي الشفرات رديئة الجودة إلى زيادة الاحتكاك والإجهاد الحراري، مما قد يؤدي إلى تشققات أو تشققات. لذا، يُعد اختيار مادة الشفرة المناسبة أمرًا بالغ الأهمية. -أداء سائل التبريدتساعد سوائل التبريد على خفض درجة حرارة القطع، وتقليل الاحتكاك، وإزالة الشوائب. قد يؤدي عدم كفاءة سوائل التبريد إلى ارتفاع درجات الحرارة وتراكم الشوائب، مما يؤثر على جودة القطع وكفاءته. لذا، يُعد اختيار سوائل تبريد فعّالة وصديقة للبيئة أمرًا بالغ الأهمية. | تؤثر جودة الشفرة على دقة ونعومة القطع. قد يؤدي استخدام سائل تبريد غير فعال إلى ضعف جودة وكفاءة القطع، مما يُبرز الحاجة إلى الاستخدام الأمثل لسائل التبريد. |
مراقبة العمليات وفحص الجودة | -التحكم في العمليات:مراقبة وتعديل معلمات القطع الرئيسية في الوقت الفعلي لضمان الاستقرار والاتساق في عملية القطع. -فحص الجودة:تساعد عمليات فحص المظهر بعد القطع، والقياسات الأبعادية، واختبارات الأداء الكهربائي في تحديد مشكلات الجودة ومعالجتها على الفور، مما يؤدي إلى تحسين دقة القطع وتناسقها. | تساعد مراقبة العملية المناسبة وفحص الجودة على ضمان الحصول على نتائج قطع متسقة وعالية الجودة والكشف المبكر عن المشكلات المحتملة. |

تحسين جودة القطع
يتطلب تحسين جودة القطع اتباع نهج شامل يأخذ في الاعتبار معايير العملية، واختيار المعدات والمواد، ومراقبة العملية، والفحص. ومن خلال التطوير المستمر لتقنيات القطع وتحسين أساليب المعالجة، يمكن تعزيز دقة واستقرار قطع الرقاقات، مما يوفر دعمًا فنيًا أكثر موثوقية لصناعة تصنيع أشباه الموصلات.
#03 التعامل والاختبار بعد القطع
3.1 التنظيف والتجفيف
تُعد خطوات التنظيف والتجفيف بعد قطع الرقاقة أساسية لضمان جودة الرقاقة وسلاسة سير العمليات اللاحقة. خلال هذه المرحلة، من الضروري إزالة بقايا السيليكون وبقايا سائل التبريد والملوثات الأخرى الناتجة عن القطع تمامًا. ومن المهم أيضًا ضمان عدم تلف الرقاقات أثناء عملية التنظيف، وبعد التجفيف، التأكد من عدم وجود أي رطوبة على سطح الرقاقة لمنع مشاكل مثل التآكل أو التفريغ الكهروستاتيكي.
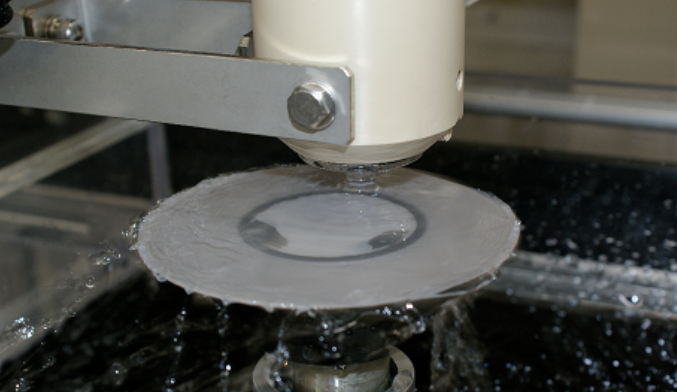
معالجة ما بعد القطع: عملية التنظيف والتجفيف
خطوة العملية | محتوى | تأثير |
عملية التنظيف | -طريقة:استخدم مواد التنظيف المتخصصة والمياه النقية، جنبًا إلى جنب مع تقنيات التنظيف بالموجات فوق الصوتية أو الميكانيكية. | يضمن الإزالة الكاملة للملوثات ويمنع تلف الرقائق أثناء التنظيف. |
-اختيار عامل التنظيف:اختر بناءً على مادة الرقاقة ونوع الملوث لضمان التنظيف الفعال دون إتلاف الرقاقة. | يعد اختيار الوكيل المناسب أمرًا أساسيًا للتنظيف الفعال وحماية الرقائق. | |
-التحكم في المعلمات:التحكم بشكل صارم في درجة حرارة التنظيف والوقت وتركيز محلول التنظيف لمنع مشاكل الجودة الناجمة عن التنظيف غير السليم. | تساعد عناصر التحكم على تجنب إتلاف الرقاقة أو ترك الملوثات خلفها، مما يضمن الجودة الثابتة. | |
عملية التجفيف | -الطرق التقليدية:التجفيف بالهواء الطبيعي والتجفيف بالهواء الساخن، والتي لها كفاءة منخفضة ويمكن أن تؤدي إلى تراكم الكهرباء الساكنة. | قد يؤدي ذلك إلى أوقات تجفيف أبطأ ومشاكل ثابتة محتملة. |
-التقنيات الحديثة:استخدم تقنيات متقدمة مثل التجفيف بالتفريغ والتجفيف بالأشعة تحت الحمراء لضمان جفاف الرقائق بسرعة وتجنب التأثيرات الضارة. | عملية تجفيف أسرع وأكثر كفاءة، مما يقلل من خطر التفريغ الساكن أو المشاكل المتعلقة بالرطوبة. | |
اختيار المعدات والصيانة | -اختيار المعدات:تعمل آلات التنظيف والتجفيف عالية الأداء على تحسين كفاءة المعالجة والتحكم بدقة في المشكلات المحتملة أثناء التعامل. | تضمن الآلات عالية الجودة معالجة أفضل وتقلل من احتمالية حدوث أخطاء أثناء التنظيف والتجفيف. |
-صيانة المعدات:إن الفحص والصيانة المنتظمة للمعدات تضمن بقائها في حالة عمل مثالية، مما يضمن جودة الشريحة. | تمنع الصيانة المناسبة فشل المعدات، مما يضمن معالجة موثوقة وعالية الجودة. |
التنظيف والتجفيف بعد القطع
تُعد خطوات التنظيف والتجفيف بعد قطع الرقاقة عمليات معقدة ودقيقة تتطلب دراسة متأنية لعوامل متعددة لضمان نتيجة المعالجة النهائية. وباستخدام أساليب علمية وإجراءات دقيقة، يُمكن ضمان دخول كل رقاقة إلى مراحل التغليف والاختبار اللاحقة في حالة مثالية.
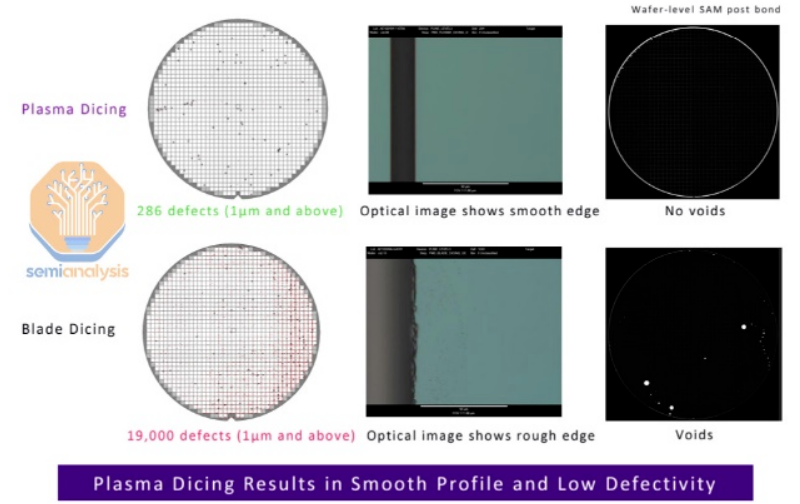
الفحص والاختبار بعد القطع
خطوة | محتوى | تأثير |
خطوة التفتيش | 1.التفتيش البصرياستخدم معدات فحص بصرية أو آلية للتحقق من وجود عيوب ظاهرة، مثل الشقوق أو التشققات أو التلوث، على سطح الشريحة. حدد بسرعة الرقائق التالفة ماديًا لتجنب الهدر. | يساعد في تحديد وإزالة الرقائق المعيبة في وقت مبكر من العملية، مما يقلل من فقدان المواد. |
2.قياس الحجم:استخدم أجهزة قياس دقيقة لقياس أبعاد الشريحة بشكل دقيق، مما يضمن أن حجم القطع يلبي مواصفات التصميم ويمنع مشكلات الأداء أو صعوبات التعبئة والتغليف. | ضمان أن تكون الرقائق ضمن حدود الحجم المطلوبة، ومنع تدهور الأداء أو مشاكل التجميع. | |
3.اختبار الأداء الكهربائي:تقييم المعلمات الكهربائية الرئيسية مثل المقاومة والسعة والمحاثة، لتحديد الرقائق غير المطابقة والتأكد من أن الرقائق المؤهلة للأداء فقط هي التي تنتقل إلى المرحلة التالية. | يضمن فقط أن الشرائح الوظيفية والمختبرة الأداء هي التي تتحرك للأمام في العملية، مما يقلل من خطر الفشل في المراحل اللاحقة. | |
خطوة الاختبار | 1.الاختبار الوظيفي:التأكد من أن الوظيفة الأساسية للشريحة تعمل كما هو مقصود، وذلك من خلال تحديد الشرائح التي بها خلل وظيفي والقضاء عليها. | ضمان أن الرقائق تلبي متطلبات التشغيل الأساسية قبل الانتقال إلى المراحل اللاحقة. |
2.اختبار الموثوقية:تقييم استقرار أداء الشريحة في ظل الاستخدام لفترات طويلة أو البيئات القاسية، والذي يتضمن عادةً الشيخوخة في درجات حرارة عالية، واختبار درجات حرارة منخفضة، واختبار الرطوبة لمحاكاة الظروف القاسية في العالم الحقيقي. | يضمن أن الرقائق يمكن أن تعمل بشكل موثوق في ظل مجموعة من الظروف البيئية، مما يحسن عمر المنتج واستقراره. | |
3.اختبار التوافق:تأكد من أن الشريحة تعمل بشكل صحيح مع المكونات أو الأنظمة الأخرى، مع التأكد من عدم وجود أي أعطال أو انخفاض في الأداء بسبب عدم التوافق. | يضمن التشغيل السلس في التطبيقات الواقعية من خلال منع مشكلات التوافق. |
3.3 التعبئة والتغليف والتخزين
بعد قطع الرقاقة، تُعدّ الرقاقات جزءًا أساسيًا من عملية تصنيع أشباه الموصلات، كما أن مراحل تغليفها وتخزينها لا تقل أهمية. وتُعدّ إجراءات التغليف والتخزين المناسبة أساسية ليس فقط لضمان سلامة الرقاقات واستقرارها أثناء النقل والتخزين، بل أيضًا لتوفير دعم قوي لمراحل الإنتاج والاختبار والتغليف اللاحقة.
ملخص مراحل التفتيش والاختبار:
تشمل خطوات فحص واختبار الرقائق بعد قطعها جوانب متعددة، بما في ذلك الفحص البصري، وقياس الحجم، واختبار الأداء الكهربائي، والاختبار الوظيفي، واختبار الموثوقية، واختبار التوافق. هذه الخطوات مترابطة ومتكاملة، وتشكل حاجزًا قويًا لضمان جودة المنتج وموثوقيته. ومن خلال إجراءات فحص واختبار صارمة، يمكن تحديد المشاكل المحتملة وحلها بسرعة، مما يضمن تلبية المنتج النهائي لمتطلبات العملاء وتوقعاتهم.
وجه | محتوى |
تدابير التعبئة والتغليف | 1.مضاد للكهرباء الساكنة:يجب أن تتمتع مواد التغليف بخصائص مضادة للكهرباء الساكنة ممتازة لمنع الكهرباء الساكنة من إتلاف الأجهزة أو التأثير على أدائها. |
2.مقاوم للرطوبة:يجب أن تتمتع مواد التغليف بمقاومة جيدة للرطوبة لمنع التآكل وتدهور الأداء الكهربائي الناتج عن الرطوبة. | |
3.مقاوم للصدمات:يجب أن توفر مواد التغليف امتصاصًا فعالًا للصدمات لحماية الرقائق من الاهتزاز والصدمات أثناء النقل. | |
بيئة التخزين | 1.التحكم في الرطوبة:التحكم الصارم في الرطوبة ضمن نطاق مناسب لمنع امتصاص الرطوبة والتآكل الناجم عن الرطوبة الزائدة أو المشكلات الثابتة الناجمة عن انخفاض الرطوبة. |
2.نظافة:الحفاظ على بيئة تخزين نظيفة لتجنب تلوث الرقائق بالغبار والشوائب. | |
3.التحكم في درجة الحرارة:قم بتحديد نطاق معقول لدرجة الحرارة والحفاظ على استقرار درجة الحرارة لمنع الشيخوخة السريعة بسبب الحرارة الزائدة أو مشاكل التكثيف الناجمة عن درجات الحرارة المنخفضة. | |
التفتيش الدوري | افحص الرقائق المُخزَّنة وقيّمها بانتظام، باستخدام عمليات الفحص البصري، وقياسات الحجم، واختبارات الأداء الكهربائي، لتحديد المشاكل المحتملة ومعالجتها في الوقت المناسب. بناءً على وقت التخزين وظروفه، خُطِّط لاستخدام الرقائق لضمان استخدامها في حالة مثالية. |
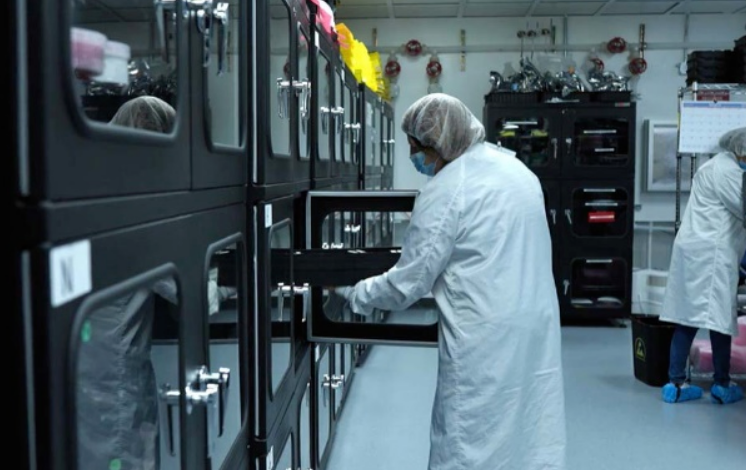
تُشكّل مشكلة التشققات الدقيقة والتلف أثناء عملية تقطيع الرقاقة تحديًا كبيرًا في تصنيع أشباه الموصلات. ويُعدّ إجهاد القطع السبب الرئيسي لهذه الظاهرة، إذ يُحدث شقوقًا صغيرة وأضرارًا على سطح الرقاقة، مما يؤدي إلى زيادة تكاليف التصنيع وانخفاض جودة المنتج.
لمواجهة هذا التحدي، من الضروري تقليل إجهاد القطع وتطبيق تقنيات وأدوات وظروف قطع مُحسّنة. إن الاهتمام الدقيق بعوامل مثل مادة الشفرة، وسرعة القطع، والضغط، وطرق التبريد، يمكن أن يُساعد في تقليل تكوّن الشقوق الدقيقة، وتحسين الإنتاجية الإجمالية للعملية. بالإضافة إلى ذلك، تُجري الأبحاث الجارية في تقنيات القطع الأكثر تطورًا، مثل التقطيع بالليزر، لاستكشاف سبل التخفيف من هذه المشكلات بشكل أكبر.
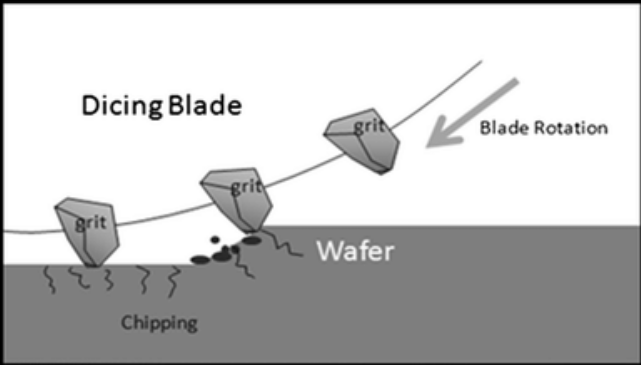
نظرًا لكونها مادة هشة، فإن الرقائق عرضة للتغيرات الهيكلية الداخلية عند تعرضها لإجهاد ميكانيكي أو حراري أو كيميائي، مما يؤدي إلى تكوّن شقوق مجهرية. ورغم أن هذه الشقوق قد لا تُلاحظ فورًا، إلا أنها قد تتوسع وتُسبب أضرارًا جسيمة مع تقدم عملية التصنيع. وتزداد هذه المشكلة تعقيدًا خلال مراحل التغليف والاختبار اللاحقة، حيث يمكن أن تؤدي تقلبات درجات الحرارة والإجهادات الميكانيكية الإضافية إلى تطور هذه الشقوق الدقيقة إلى كسور مرئية، مما قد يؤدي إلى فشل الرقاقة.
للحد من هذا الخطر، من الضروري التحكم في عملية القطع بدقة من خلال تحسين معايير مثل سرعة القطع والضغط ودرجة الحرارة. استخدام أساليب قطع أقل حدة، مثل التقطيع بالليزر، يُخفف الضغط الميكانيكي على الرقاقة ويُقلل من تكوّن الشقوق الدقيقة. إضافةً إلى ذلك، فإن استخدام أساليب فحص متقدمة، مثل المسح بالأشعة تحت الحمراء أو التصوير بالأشعة السينية أثناء عملية تقطيع الرقاقة، يُساعد في الكشف عن هذه الشقوق في مراحلها المبكرة قبل أن تُسبب المزيد من الضرر.
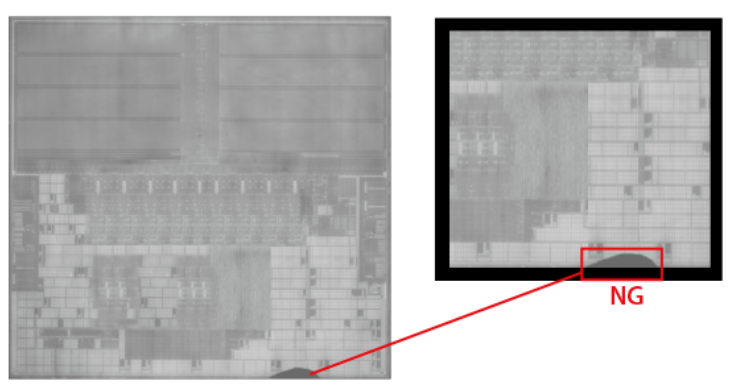
يُعد تلف سطح الرقاقة مصدر قلق بالغ في عملية التقطيع، إذ قد يؤثر بشكل مباشر على أداء الرقاقة وموثوقيتها. قد ينتج هذا التلف عن سوء استخدام أدوات القطع، أو معايير قطع غير صحيحة، أو عيوب في مادة الرقاقة نفسها. وبغض النظر عن السبب، قد تؤدي هذه التلفيات إلى تغيرات في المقاومة الكهربائية أو سعة الدائرة، مما يؤثر على الأداء العام.
ولمعالجة هذه القضايا، يجري استكشاف استراتيجيتين رئيسيتين:
1. تحسين أدوات القطع والمعلمات:من خلال استخدام شفرات أكثر حدة، وضبط سرعة القطع، وتعديل عمق القطع، يمكن تقليل تركيز الضغط أثناء عملية القطع، وبالتالي تقليل احتمالية حدوث الضرر.
2.استكشاف تقنيات القطع الجديدةتُحسّن التقنيات المتقدمة، مثل القطع بالليزر والبلازما، دقة القطع مع إمكانية تقليل مستوى الضرر الواقع على الرقاقة. وتُدرس هذه التقنيات لإيجاد طرق لتحقيق دقة قطع عالية مع تقليل الضغط الحراري والميكانيكي على الرقاقة.
منطقة التأثير الحراري وتأثيراتها على الأداء
في عمليات القطع الحراري، كالقطع بالليزر والبلازما، تُنشئ درجات الحرارة المرتفعة حتمًا منطقة تأثير حراري على سطح الرقاقة. هذه المنطقة، التي يكون فيها التفاوت في درجة الحرارة كبيرًا، قد تُغير خصائص المادة، مما يؤثر على الأداء النهائي للرقاقة.
تأثير المنطقة المتأثرة بالحرارة (TAZ):
تغيرات البنية البلوريةفي درجات الحرارة المرتفعة، قد تتجدد الذرات داخل مادة الرقاقة، مما يُسبب تشوهات في البنية البلورية. يُضعف هذا التشويه المادة، ويُقلل من قوتها الميكانيكية واستقرارها، مما يزيد من خطر تلف الرقاقة أثناء الاستخدام.
التغيرات في الخصائص الكهربائيةيمكن أن تُغير درجات الحرارة المرتفعة تركيز الناقلات وحركتها في مواد أشباه الموصلات، مما يؤثر على موصلية الشريحة الكهربائية وكفاءة نقل التيار. قد تؤدي هذه التغييرات إلى انخفاض أداء الشريحة، مما قد يجعلها غير صالحة للغرض المقصود منها.
ولتخفيف هذه التأثيرات، فإن التحكم في درجة الحرارة أثناء القطع، وتحسين معلمات القطع، واستكشاف طرق مثل نفثات التبريد أو معالجات ما بعد المعالجة، كلها استراتيجيات أساسية لتقليل مدى التأثير الحراري والحفاظ على سلامة المواد.
بشكل عام، تُعدّ الشقوق الدقيقة ومناطق التأثير الحراري تحدياتٍ جوهرية في تقنية تقطيع الرقائق. وسيكون من الضروري مواصلة البحث، إلى جانب التطورات التكنولوجية وإجراءات مراقبة الجودة، لتحسين جودة منتجات أشباه الموصلات وتعزيز قدرتها التنافسية في السوق.
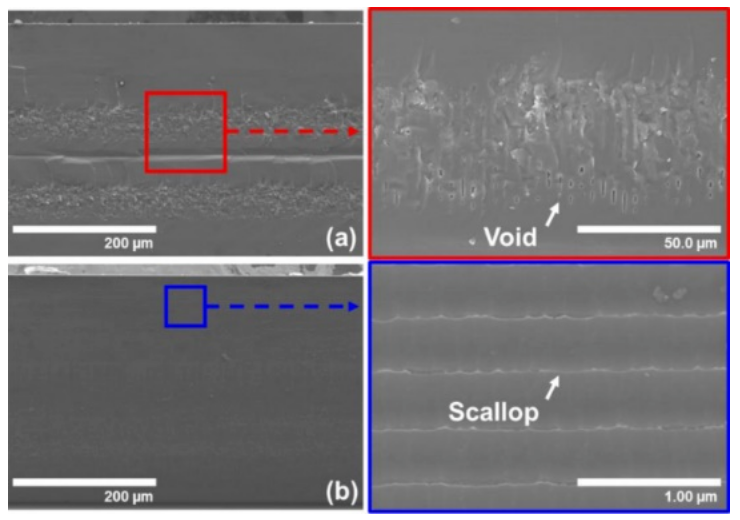
التدابير للسيطرة على منطقة التأثير الحراري:
تحسين معلمات عملية القطع:يمكن أن يؤدي تقليل سرعة القطع وقوته إلى تقليل حجم منطقة التأثير الحراري (TAZ) بشكل فعال. يساعد هذا في التحكم في كمية الحرارة المتولدة أثناء عملية القطع، مما يؤثر بشكل مباشر على خصائص مادة الرقاقة.
تقنيات التبريد المتقدمةيُمكن لتطبيق تقنيات مثل تبريد النيتروجين السائل والتبريد الميكروفلويدي أن يُحدّ بشكل كبير من نطاق منطقة التأثير الحراري. تُساعد طرق التبريد هذه على تبديد الحرارة بكفاءة أكبر، مما يُحافظ على خصائص مادة الرقاقة ويُقلّل من الضرر الحراري.
اختيار المواديستكشف الباحثون مواد جديدة، مثل أنابيب الكربون النانوية والجرافين، تتميز بموصلية حرارية ممتازة ومتانة ميكانيكية. ويمكن لهذه المواد تقليل منطقة التأثير الحراري مع تحسين الأداء العام للرقائق.
باختصار، على الرغم من أن منطقة التأثير الحراري نتيجة حتمية لتقنيات القطع الحراري، إلا أنه يمكن التحكم فيها بفعالية من خلال تقنيات المعالجة المُحسّنة واختيار المواد المُناسبة. ومن المرجح أن تُركز الأبحاث المستقبلية على ضبط عمليات القطع الحراري وأتمتتها لتحقيق تقطيع رقائق أكثر كفاءة ودقة.

استراتيجية التوازن:
يُعدّ تحقيق التوازن الأمثل بين إنتاجية الرقاقات وكفاءة الإنتاج تحديًا مستمرًا في تكنولوجيا تقطيع الرقاقات. ويتعين على المصنّعين مراعاة عوامل متعددة، مثل طلب السوق وتكاليف الإنتاج وجودة المنتج، لوضع استراتيجية إنتاج ومعايير عملية رشيدة. وفي الوقت نفسه، يُعدّ إدخال معدات قطع متطورة، وتحسين مهارات المشغلين، وتحسين مراقبة جودة المواد الخام، أمرًا أساسيًا للحفاظ على الإنتاجية أو حتى تحسينها مع زيادة كفاءة الإنتاج.
التحديات والفرص المستقبلية:
مع تطور تكنولوجيا أشباه الموصلات، يواجه قطع الرقاقات تحديات وفرصًا جديدة. فمع تقلص أحجام الرقاقات وزيادة التكامل، يزداد الطلب على دقة وجودة القطع بشكل ملحوظ. وفي الوقت نفسه، تُقدم التقنيات الناشئة أفكارًا جديدة لتطوير تقنيات قطع الرقاقات. ويجب على المصنّعين مواكبة ديناميكيات السوق والاتجاهات التكنولوجية، وتعديل وتحسين استراتيجيات الإنتاج ومعايير العمليات باستمرار لتلبية تغيرات السوق والمتطلبات التكنولوجية.
وفي الختام، من خلال دمج اعتبارات الطلب في السوق وتكاليف الإنتاج وجودة المنتج، ومن خلال إدخال المعدات والتكنولوجيا المتقدمة، وتعزيز مهارات المشغل، وتعزيز التحكم في المواد الخام، يمكن للمصنعين تحقيق أفضل توازن بين إنتاج الرقاقة وكفاءة الإنتاج أثناء تقطيع الرقاقة، مما يؤدي إلى إنتاج منتجات أشباه الموصلات بكفاءة وعالي الجودة.
النظرة المستقبلية:
مع التطورات التكنولوجية السريعة، تتقدم تكنولوجيا أشباه الموصلات بوتيرة غير مسبوقة. وباعتبارها خطوةً حاسمةً في تصنيع أشباه الموصلات، فإن تقنية قطع الرقاقات مهيأةٌ لتطوراتٍ جديدةٍ ومثيرة. وبالنظر إلى المستقبل، من المتوقع أن تحقق هذه التقنية تحسيناتٍ كبيرةً في الدقة والكفاءة والتكلفة، مما يُضفي حيويةً جديدةً على النمو المستمر لصناعة أشباه الموصلات.
زيادة الدقة:
في سعيها لتحقيق دقة أعلى، ستواصل تقنية قطع الرقاقات تجاوز حدود العمليات الحالية. من خلال الدراسة المتعمقة للآليات الفيزيائية والكيميائية لعملية القطع والتحكم الدقيق في معاملات القطع، سيتم تحقيق نتائج قطع أدق لتلبية متطلبات تصميم الدوائر المتزايدة التعقيد. بالإضافة إلى ذلك، سيؤدي استكشاف مواد وطرق قطع جديدة إلى تحسين الإنتاجية والجودة بشكل كبير.
تعزيز الكفاءة:
ستركز معدات قطع الرقاقات الجديدة على التصميم الذكي والآلي. سيُمكّن إدخال أنظمة التحكم والخوارزميات المتقدمة المعدات من ضبط معلمات القطع تلقائيًا لتناسب مختلف المواد ومتطلبات التصميم، مما يُحسّن كفاءة الإنتاج بشكل ملحوظ. وستلعب ابتكارات مثل تقنية قطع الرقاقات المتعددة وأنظمة استبدال الشفرات السريعة دورًا حاسمًا في تعزيز الكفاءة.
خفض التكاليف:
يُعد خفض التكاليف توجهًا رئيسيًا لتطوير تقنية قطع الرقاقات. ومع تطوير مواد وطرق قطع جديدة، من المتوقع التحكم بفعالية في تكاليف المعدات ونفقات الصيانة. إضافةً إلى ذلك، سيؤدي تحسين عمليات الإنتاج وخفض معدلات الخردة إلى تقليل الهدر أثناء التصنيع، مما يؤدي إلى انخفاض إجمالي تكاليف الإنتاج.
التصنيع الذكي وإنترنت الأشياء:
سيُحدث دمج تقنيات التصنيع الذكي وإنترنت الأشياء (IoT) تغييرات جذرية في تقنية قطع الرقائق. فمن خلال الترابط وتبادل البيانات بين الأجهزة، يُمكن مراقبة كل خطوة من خطوات عملية الإنتاج وتحسينها آنيًا. وهذا لا يُحسّن كفاءة الإنتاج وجودة المنتج فحسب، بل يُتيح للشركات أيضًا تنبؤات سوقية أكثر دقة ودعمًا لاتخاذ القرارات.
في المستقبل، ستُحرز تقنية قطع الرقاقات تقدمًا ملحوظًا في الدقة والكفاءة والتكلفة. ستدفع هذه التطورات عجلة التطور المستمر لصناعة أشباه الموصلات، وستجلب المزيد من الابتكارات التكنولوجية والتسهيلات للمجتمع البشري.
وقت النشر: ١٩ نوفمبر ٢٠٢٤